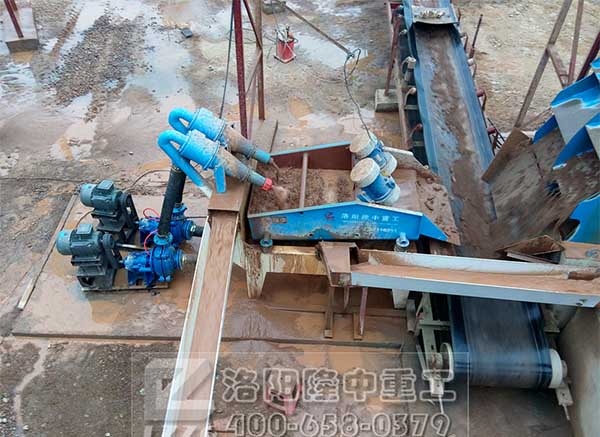
20 tph sand washing and dewatering screen for sale
The widespread use of machine-made sand has made the sand ma…
Tel: 86-18736301510
Fax: 86-379-65160018
Email: export@lylzzg.com
2021-07-03
In the actual working process of the coal gangue vibrating banana screen, the screen surface at the end of the banana screen is often blocked by large-size materials. Therefore, workers need to be arranged next to each vibrating screen to manually remove the screen holes, which not only increases the cost of the company, but also It is easy to cause the health of workers to be damaged by dust. In addition, due to the large size of the material, the material and the large gangue in it will have a direct impact on the conveyor belt during transportation. Therefore, the entire conveyor belt of the vibrating banana screen is prone to damage when running under severe working conditions, and the conveyor belt needs to be replaced constantly, which adds a lot of cost to the factory.
In view of the problem of easy clogging of sieve holes, there are many factors related to the sieve penetration rate, including the size and structure of the sieve, the size and shape of the material, the direction of the sieve plate layout, and the amplitude of the banana sieve. Therefore, it is necessary to comprehensively consider these factors and optimize the parameters to achieve the optimal penetration rate.
1. Reduce the gap between the feeding end of the screen and the screen plate. After raising the position of the feeding end of the sieve machine, the inclination angle of the sieve machine is increased, thereby accelerating the initial movement speed of the material, enhancing the movement inertia, and improving the screen penetration rate of the material. However, this solution increases the material movement speed while reducing the time that the material stays on the screen surface. For small-sized materials (below 50mm), the material will directly enter the material collection funnel, resulting in a decrease and increase in the penetration rate of the material. The number of times the material was screened. At the same time, the workload of the collection funnel is increased, and the funnel also needs to be modified. Or reduce the height of the discharge end, which will cause the same problem as increasing the position of the feed end of the screen, but relatively speaking, there is no need to modify the funnel, and it can also reduce the impact of the material on the conveyor belt.
2. Optimize the size and shape of screen holes. The sieve surface of the banana sieve is usually made of punching holes, and there are two kinds of sieve holes in the shape of round holes and capsule. The basic material blocking the sieve holes is the sieve plate with round sieve holes. Therefore, changing the shape of the sieve holes and designing elliptical or rectangular sieve holes can effectively improve the material penetration rate through practical operation. However, due to the change in the shape of the sieve hole, a small part of the material that matches the shape of the sieve hole will also pass through the sieve, causing a part of the material waste and increasing the burden of the subsequent process.
3. Change the amplitude of the sieve machine. By increasing the amplitude, the material conveying speed can be increased, and the material can stay on the sieve plate for a long time and cause the sieve hole to be blocked. This scheme can increase the vibration amplitude of the screen by increasing the excitation force. However, due to the increase in the amplitude, the life of the screen will be reduced.
In addition, for the problem of materials impacting the conveyor belt. The following methods can be used: (1) Reduce the height difference between the conveyor and the discharge end; (2) Design a buffer belt on the conveyor belt and the discharge end; (3) Relax the conveyor belt and use the elasticity of the belt to cushion the impact of materials .